Soporte Sigma archivos open source
Introduction
Having a look on the BCN3D Sigma files, you may discover many features and design details that will create tons of questions. Why did they get a dual independent extruder? Why an aluminium frame? Custom electronics?… We didn’t want to just upload a CAD file, some gerber and firmware files. We wanted to give to the community an explanation of the solutions we chose, the “behind the scenes” of these solutions.
BCN3D Technologies is a division that belongs to the Fundació CIM. This last entity is a long time experienced technological center located in Barcelona mainly specialized in advanced manufacturing. Fundacio CIM has SLA and SLS rapid prototyping machines since late 90’s.
One of the aims of Fundació, as a non-profit foundation, is to spread the knowledge in technology in the territory. Fundació CIM offers a real experience for students coming from the university (most of them from UPC) but, more importantly, it gives the companies in Catalunya and Spain the possibility to see, learn and even order services in fabrication technologies they wouldn’t be able to afford by themselves.
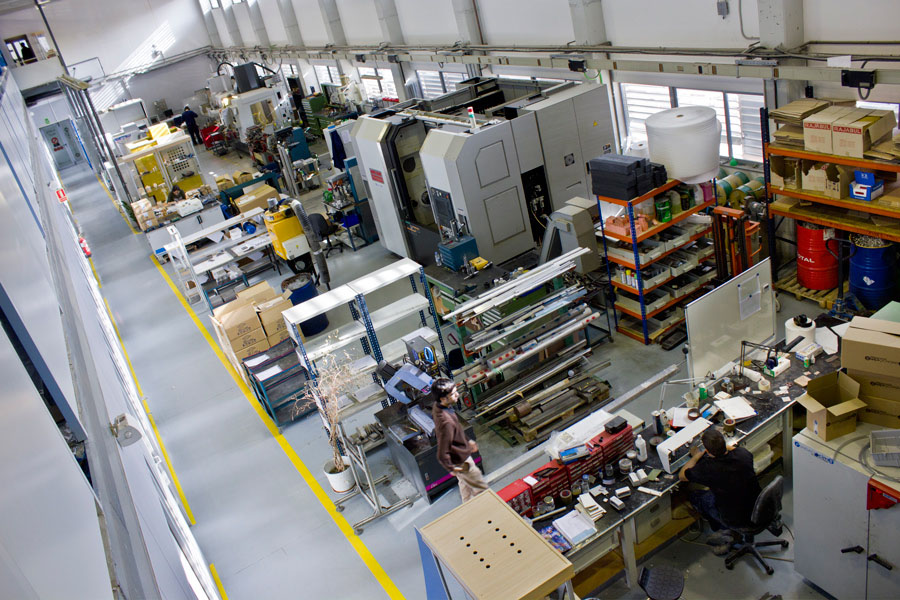
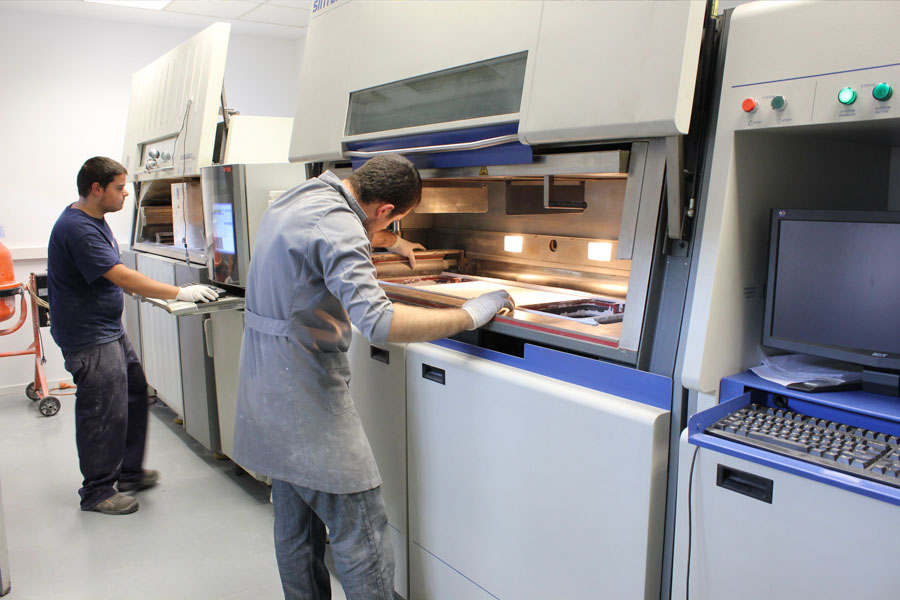
This seems not to have any relation with the BCN3D Sigma but in fact is the main reason for it to exist. When we started working in the RepRap project under the name RepRapBCN in 2011, visitors coming to Fundacio CIM were amazed by the simplicity of those little machines made with rods, bolts and nuts. They were able to see something not visible in the big rapid prototyping machines: How the part is made.
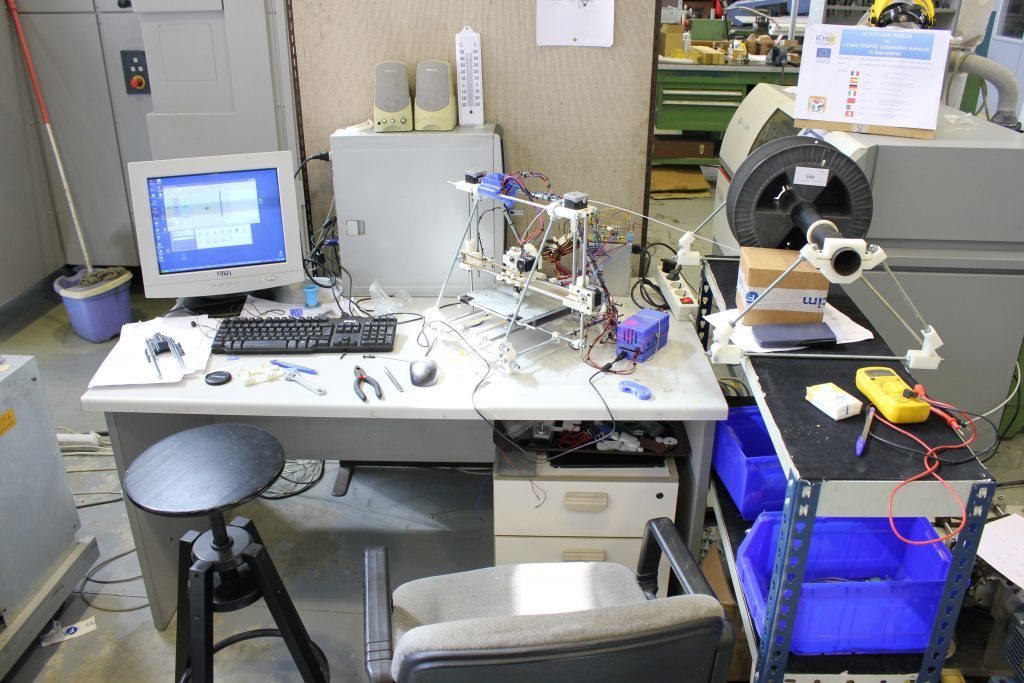
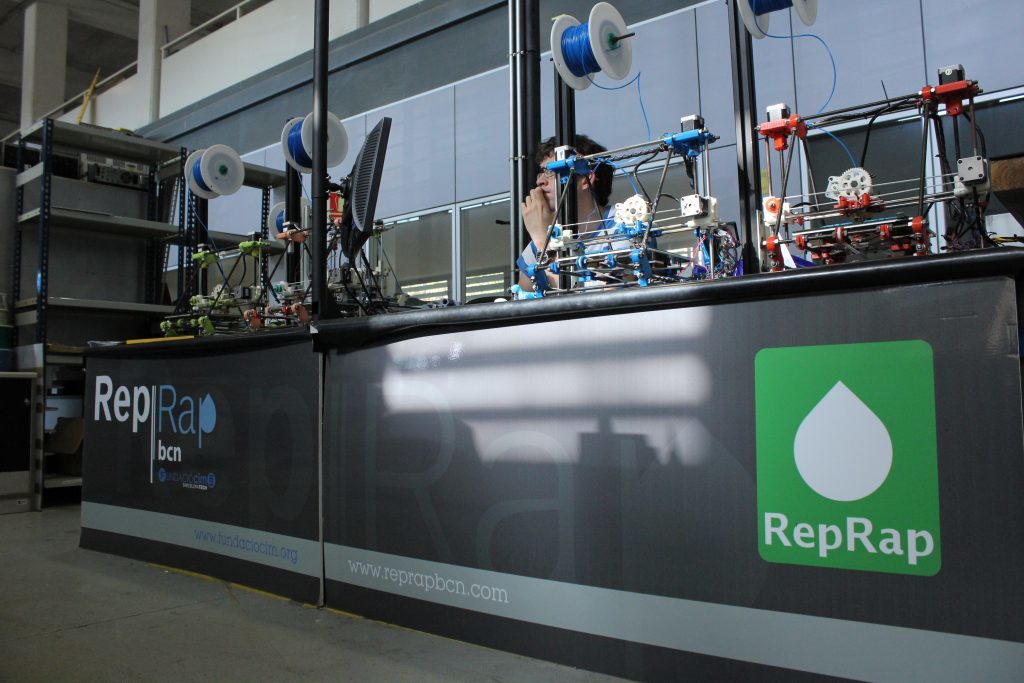
But they also saw something undesirable: Those RepRap Machines were unreliable when used intensively. Moreover, the quality of the outcoming parts was far away from the professional technologies results. In addition, there were serious geometric limitations, so many real-world parts couldn’t be produced. None of those visitors could become users: they did expected better features.
The influence of the big sisters, the SLS and the SLA, as well as the suggestions of the visitors, made us try to solve those problems and shorten the distance between professional rapid prototyping machines and the RepRapBCN machines. Before starting to invent new machines, though, we would try to get the best of the RepRap concept.
The BCN3D+ was designed in the 2013. An upgrade was available for experimented users to start printing with two extruders. At that moment it was not common a printer with two hotends, but there was enough information in the RepRap project to get the mechanics and the firmware adaptation done. So we did it.
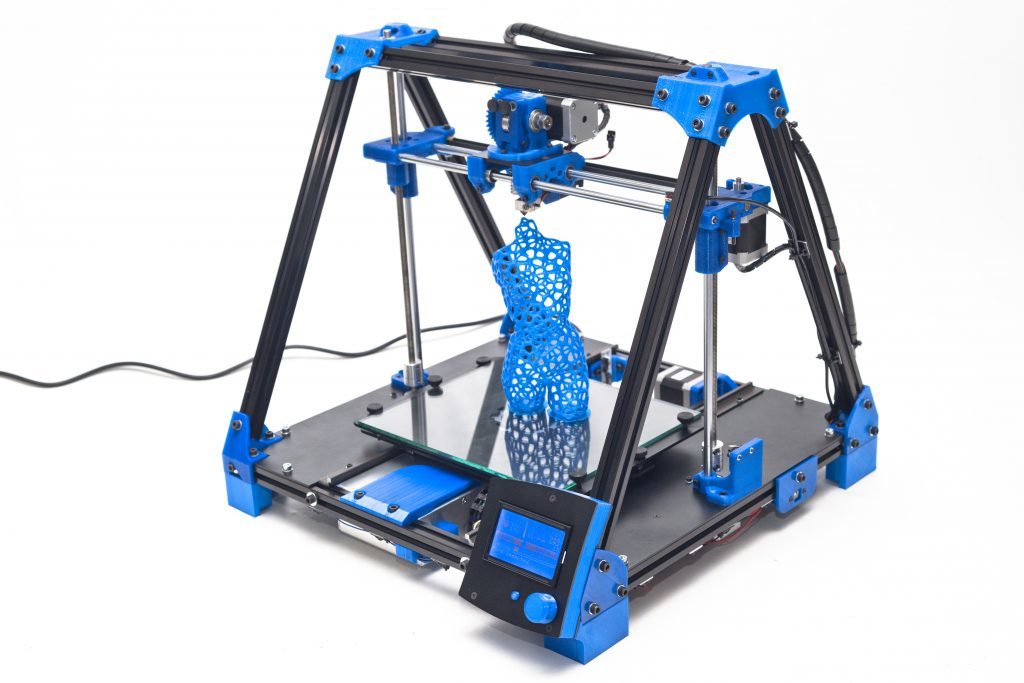
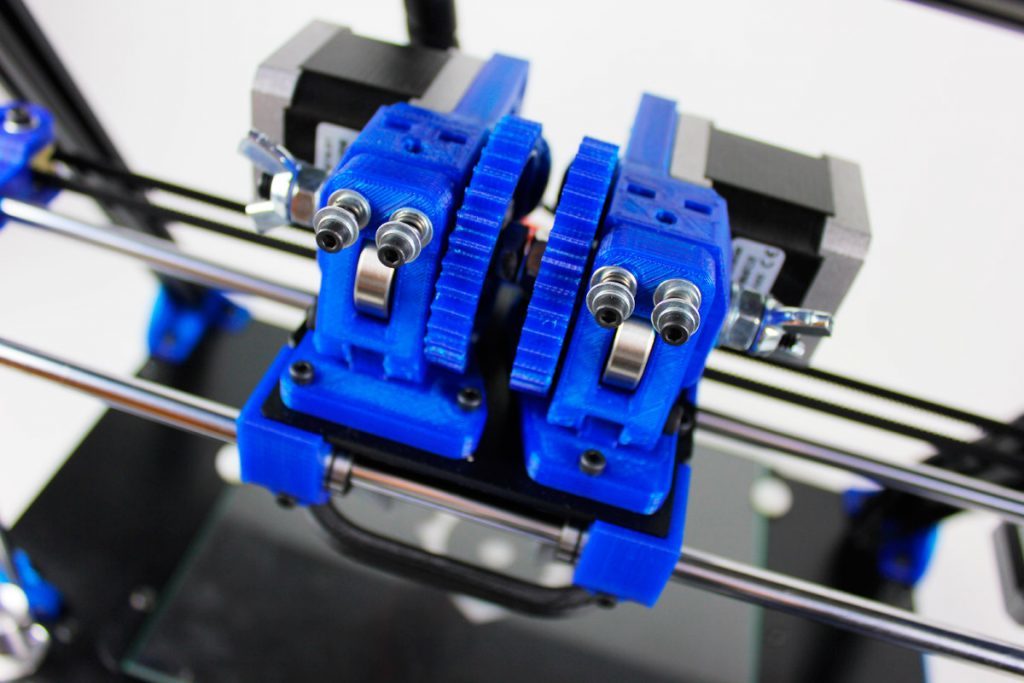
Results were a little disappointing. We achieved the fact of printing with two materials but we had many other problems related with the process: Carriage was heavy and quality in the final part was lower than the one obtained from single extruder printing. The calibration process was complex and not understandable for new users. Finally, the oozing from the idle nozzle affected the part when the other nozzle was working.
As you may know, by that time, 3D printing was the most followed technology and the hype was extreme. By the middle of 2014 we realized that the BCN3D+ was not able to fulfill the new customers that were embracing the technology. So we started a new design.
It is funny now to remember the first concept for the Sigma: A cubic machine made in aluminium profiles. Something that was clearly and upgrade of the BCN3D+.
But the disrupting point was that our chief engineer found a video in youtube of somebody printing with independent nozzles. That concept was able to solve many of the problems we had with the dual extruder upgrade we tried in the BCN3D+. Finally we had found something that would possibly make those visitors become future users and the big sisters RP machines less big. We only had to do it reliable when sold in large numbers. Only…
All the design process was conditioned by the dual printing concept. We needed something more sturdy than assembled aluminium profiles, so we designed this aluminium welded frame. We needed an easy calibration for the more complex architecture, then we added a LCD touch screen able to guide the user through the process. We needed electronics able to rule 6 axis and be reliable so we designed custom electronics… Everything on the machine is intended to make this independent dual extruder easy to operate, understand and maintain.
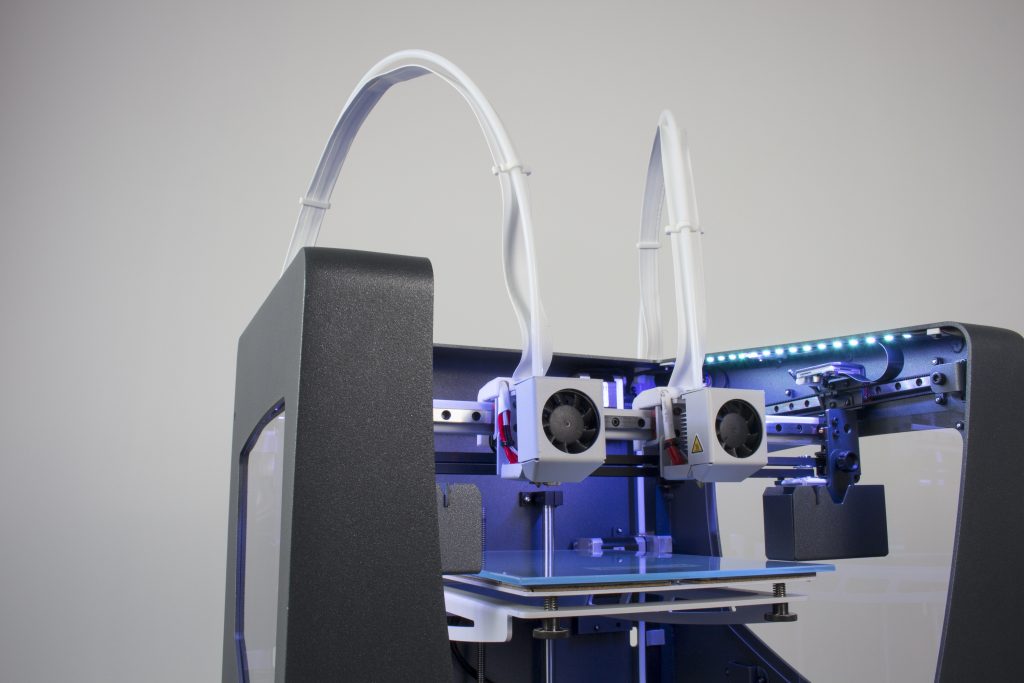
In the specific repositories you will find technical details in those solutions that had made this dual extruder system possible and the files will supporting this explanation.
Mechanics
What’s hold in this repository?
This repository will hold all the information about the Mechanics of the BCN3D Sigma.
As a declared Open Source organization, it’s in our mission to release all the original design files to you to be able to learn, reuse and improve. Open Source not only means code, it also concerns hardware.
We’ve managed to design and manufacture the BCN3D Sigma thanks to our previous experience in the 3D printing industry, the ideas coming from the community, our engineering background and a narrow collaboration with our suppliers. Our goal is justify the decisions we took and share the know-how we acquired so far.
We also provide the source files for those who want to check the core of the BCN3D Sigma. You can consult both the CAD files and the technical drawings.
Concept design
During the concept design stage we set a clear target which determined the whole design and decisions: The BCN3D Sigma is a professional printer.
Aesthetics
It has to look like a professional equipment. Our previous printers were made with aluminium extruded profiles and plastic printed parts. That made sense for printers oriented to makers or schools, sold as a kit. But, in this case, aesthetic was a major player. For this reason, we adopted a welded aluminium frame, which allows the Sigma to be a unique and attractive 3D printer.
Multimaterial
As a professional printer, it has to print as many materials as possible. Not only for engineers, who require tough -or flexible-, functional polymers, but also for designers who need the aesthetic component. However, material is not the only limitation. Complex geometries, overhangs and 3D printing doesn’t get along. So we wanted the Sigma to be a real solution for those users who need to print with supports as a must. In conclusion, the Sigma is the first and only commercial 3D printer with an Independent Dual Extuder (IDEX) system, which avoid all the side problems dual extrusion may cause.
High Quality
The 3D Printing industry is maturing. Users are more and more demanding and 3D printing must be a solution, not a headache. For this reason, the Sigma has to be a reliable piece of engineering, easy to assemble, maintain and capable to print seamlessly high quality objects, no matter how complex they are.
High Capacity
Real-life and functional parts are not always small. A big printing volume is a great advantage for a professional 3D Printer although the Sigma intends to be a desktop-sized printer. Allocating all the items and devices inside the frame, while granting ease-to-use and optimizing the axes structure were a key goal.
Detail design insights
We faced dozens of challenges during the design process. Below we describe some of them:
Frame
Probably the biggest challenge. First we thought in a chassis made of profiles and then cover it. But then realized the cost in materials for that solution would be high enough to look for alternatives that could contribute more in the aesthetic field, even that could be a bit more expensive. On the other side, we wanted the Sigma to be an accessible printer, wide and open in order to ease the handling and operation. So we decided to explore the option of designing a unibody frame where all the mechanical components were mounted on and with a wide frontal oberture.
First we had to decide between using aluminium or steel. Steel offers many advantages: It’s a very stiff metal, great to build structures and precise mechanical systems. In addition, it’s easy to work with and cheap. But it’s -really- heavy. We contemplated the option of using a thinner metal sheet of steel for the frame. After ordering a prototype, we dismissed the idea, though. Still it had a great mechanical behaviour and a relative low weight, the feeling of touching a thin metal sheet (1.5mm) was unpleasant because it felt like a cutting edge. And it didn’t look sturdy. So to achieve both a reliable look and a pleasant contact, we needed to go up to 3mm thickness. But then the shipping costs would be absurdly high and the handling, a constant hassle -both during the assembly process and for the final user.
Aluminium, on the other hand, provides lightness and a smooth and sturdy look. But it’s more expensive as a material and it’s harder to laser cut and weld. After balancing pros and cons, we bet on aluminium option -although we had a plan B.
The second big issue to manage was the manufacturing process. We contemplated two different ways to do it: either manufacture the frame by parts and screw them all together in the assembly line or weld the frame. Welding aluminium is hard and the welding process itself has some thermal and geometric implications that have to be considered. But it allows to reduce the assembling time dramatically while it outsources a key process.
As alternative, designing the frame as separate parts to screw together was considerably cheaper – as you save a handmade process such as welding and polishing. But the assembling of the frame and adjustment could be very delicate and incompatible with our production tag time. So the overall cost wouldn’t be that different in both options. The aesthetic component, though, would be very penalized with this alternative, because we would need to add dozens of screws on the frame.
For these reasons, we finally opted for a welded structure. We sat hours with our supplier discussing the best way to design every single part in order to grant a proper alignment between the faces that would hold the axes. Furthermore, we also studied the mechanical behaviour of the frame with some CAE studies, simulating stress and deformations during a standard usage.
High quality components
A good frame is not enough to achieve amazing results. In such a precision equipment as the Sigma, all the mechanical components play a key role. Due to the product requirements in terms of size and use of the internal space of the printer we had, we opted for a axes structure with the toolheads moving in the XY plane and an up and down moving Z axis.
With the XY plane decided to mount high precision linear guides. Despite its cost slightly higher than a system based on rods and bearings, the linear rails offer a professional look, an easy assembling and a compact package.
Regarding the Z axis, we were aware of the importance to have a robust guide system in order to avoid classic artifacts in printed parts related with a bad Z performance, such as Z wobbling. We also had experience using couplings and to connect the actuator with the leadscrew and we knew that a bad assembling could cause poor quality results. With this background, we chose using Ø12mm guide rods and a stepper motor with an inserted leadscrew. The whole system provides a high repeatability and accuracy.
Independent Dual Extrusion
A 3D printer with such an specific feature increases the design unknowns and multiplies the components. Not only the firmware and the electronics need to be highly customized, but also mechanically there are some decisions to take.
First of all, because of the multiple components to hold, the internal parts tend to be more complex than other printers. So we decided to use aluminium sheet bending technology to manufacture the inner parts. As the manufacturing tolerances are acceptable for the purposes we intend and the technology is cheap and easily scalable, we considered the technology optimum.
Two independent Extruders means have an extra moving stepper for the second toolhead, and the extra toolhead itself. On the other hand, when printing with both extruders it’s important to have a bucket to purge the idle hotends before start printing the model again. All this parts add weight to a moving element, which is a problem to print fast because the high inertias may worsen the print quality. So we designed the X and Y Axis as light as possible, saving as many grams as possible with every single component. Not only weight is important when doubling the toolheads, but also space. So we decided to adopt a bowden-based feeding system and miniaturize all the items as much as possible.
Big Printing Volume
The BCN3D Sigma features 210x297x210mm printing volume. In order to provide such a big volume and a free space on both sides to park the idle toolhead, but still having a desktop-sized printer, we had to reorient the Z platform. The main issue to solve, though, was granting the stiffness of the structure with a big overhang of more than 300mm.
To prevent vibrations, we adopted high quality bearings with low clearance and we designed and simulated a custom metal sheet structure, which allows to get a great quality prints with a smooth surface despite the big overhang.
Electronics
This repository will hold all the information about the Electronics of the BCN3D Sigma.
As a declared Open Source organization, it’s in our mission to release all the original design files to you to be able to learn, reuse and improve. Open Source not only means code, it also concerns hardware.
We’ve manage to design and manufacture our custom Electronics for the BCN3D Sigma in many ways thanks to the community an other Open Source Hardware projects. BCN3D Electronics is a mashup between the Ultimaker 2 Board, the Megatronics v3.0 and some others…
Design concept
The BCN3D Electronics is intended to be modular and custom fitted in our BCN3D Sigma 3D printer and that’s why we made some design decisions.
- Stepper drivers out of the Mainboard. As the drivers generate quite a lot of heat, we’ve moved them nearest as possible to the corresponding stepper motor. If one fails, you just have to replace a cheap stepper driver board. This way, we’ve managed to fit an entire electronics system without a fan.
- FFC’s everywhere. The BCN3D Sigma is an Independent Dual Extruder Printer so the Electronics supports 6 Axis of movement. Thats a lot of wires and wires takes some precious space. We decided to go with a Flat Flexible Cable solution that keeps things organized and it’s faster to assemble.
- 24VDC Power Supply. The performance improves as the whole Electronics run cooler while maintaining a very low voltage system.
- Full Color Resistive Touch Screen. The electronics is compatible with 4D Systems Displays out of the box. We think the user should interact with an intuitive interface to be able to use the printer easily even without previous experience in 3D printing.
Boards
- Mainboard: This board holds the microcontroller, the 5V switching power supply, the power outputs and the thermistor inputs. It has a USB interface for upgrading the firmware and communicating with the printer via serial port.
- Stepper Driver: We carry the well-known DRV8825 stepper driver from Texas Instruments. It’s able to supply plenty of power for all the types of stepper motors in the BCN3D Sigma.
- Extruder Board: It’s a simple interconnection board between the Mainboard and the components of the hotend assembly. With just one Flat Flexible Cable you the microcontroller has control over the hotend, the thermistor and endstop readings and the layer fan.
- Heated Bed: As the platform size of the BCN3D Sigma is quite big, we’ve made a custom A4 size heated bed to achieve the performance required. It can heat up to 100ºC in about 6-8 minutes and keep that temperature for long period of times.
Production
We strongly believe that using high quality components has an effect on the electronics performance as well as in the printer performance.
This is why we ensure components quality and control of the production process by designing and manufacturing in Barcelona. In this manner we iterate faster, reducing time to market.
Being in control of all the supply chain allows us to optimize designs and reduce costs.
Firmware
BCN3D Sigma Firmware based on Marlin
This is the repository that contains the firmware for the BCN3D Sigma 3D Printer. It’s based on the well-known Marlin but with some modifications.
This firmware was first programmed by Jordi Calduch then was Xavier Gómez and now Alejandro Garcia, and designed by Pedro Baños and Jaume Juan at BCN3D Technologies.
We’ve worked since the very first time with Marlin Firmware when designing the firsts BCN3D Technologies 3D printers. We’ve learnt a lot of things along the way and we feel comfortable with it and that’s the main reason to implement it on the BCN3D Sigma.
The community is huge and the project is continuously updated.
We’ve made quite a few changes to adapt it to the Sigma’s features. Here’s a list of somethings we have implemented it:
- Dual independent X extruders: one of the main features of the BCN3D Sigma is the Independent Dual EXtruder system (IDEX). It lets you print in two colors or two materials and has the ability to print support structures for your complex geometries.
- Auto-level, auto-calibration of XYZ axis: the main concern about the IDEX system is how the user will calibrate the offsets between nozzles and the bed. We’ve designed a 3 point touch pattern in order to fine tune the different axis offsets and everything is guided through the LCD display.
- LCD Touch Screen support: our goal is to get a Sigma in everybody’s hands and to do that we need to make it robust and easy to use. We think you don’t need to have previous experience in 3D printing to make gorgeous prints and adding a LCD touch screen make things easier. We’ve designed a comprehensive interface with simple menus and icons to make using the Sigma a breeze. All the code is segmented to other people take a look at it and understand it.
- Insert/Remove filament: as the printer uses a bowden based filament drive system, insert and removing the filament is an inconvenience so there’s a button to load or unload the filament. The process, once again, is guided via the touch screen and it will take you only a minute. The filament is pushed right to the tip of the nozzle.
- Refined firmware for better printing experience: Marlin firmware is well-known in the 3D Printing community as a lot of printers take benefit from it. We’re not different but we’ve tried to optimize it and take a lot of things our printer doesn’t use. As some people know, because they follow our progress on github, the code is being updated almost every day.
As we truly believe in Open Source development and we want to you knowing your machine, we document all the progress and keep track of all the issues and feedback.
Software
One of the pillars of 3D printing is the software that converts your .stl files in something your printer understands. Good software can really have an impact in the final results. That’s why we rely on the most used slicing engine and software, Cura by Ultimaker.
As the project is also open source, we’ve managed to get the code and start customizing the interface to our needs and tweaking some parameters to improve the quality of the prints.
It’s a rough way but we’re learning a lot. Every day we understand more and more why and how the printer behaves so we can keep on developing better products for you.
One of the features we’re proudest of is the automatic firmware upgrade. BCN3D Cura connects to your printer and compares your actual firmware version with the latest release in github. If there’s a newer version, the software downloads it and guide you in the process of uploading it to the printer.
This channel let us release more versions making it easy to the final users to update their printers. There’s no need to mess around with Arduino or other stuff.
We currently support BCN3D Cura for Windows and MacOS platforms. If you want to offer some help, don’t hesitate to pass by our github repositories and leave a message.
Process engineering
What’s hold in this repository?
In the present repository you will find all the documentation needed to assemble a BCN3D Sigma, from the warehouse to the box. In our commitment to Open Source, we want to be transparent, not only in the design, but also in the processes involved in the BCN3D Sigma manufacture.
Since it’s our first experience producing in an assembly line, we’ve built the structure from the ground up. In the process we have made some mistakes and faced many challenges. But day after day, we improved and deployed a solid system that is allowing us to increase month after month our production capacity in order to satisfy the growing demand.
Product Sheets
The process starts when we receive the components from our Suppliers. We check all of them in a variable proportion depending on nature of the element. Some of them, like standard mechanical or electronic components are just visually checked, while others, like custom metal sheets or electronics boards are thoroughly checked.
Kit Sheets
Since the very first day we adopted Lean Manufacturing in the Sigma assembly line. Instead of implementing a Push System, producing lots of a certain number of printers, independently of the demand, we established a Pull System, based on Kanban scheduling system, where we produce depending on the number of printers sold. In other words, the sells are “pulling” the production efforts.
This philosophy makes us more flexible and able to react to fluctuations in the demand, as well as allows us to reduce all the stocks in the production process, both the components, the semi-elaborated product and the final product.
We broke this concept apart so we planned to assemble the BCN3D Sigma in several blocks, which could be redistributed in different workstations as the production grows. The first step, though, is supplying all the material needed to each workstation and make sure it never lacks.
Therefore, we produced the “Kit Sheets”, where the components needed in every step of the assembling process are listed. Moreover, these sheets specify the quantity of kits each workstation should have to never run out of material. Finally, this document allows us to trace the key components so, at the end of the day, we know exactly the composition of a Sigma. This can help us in case we detect a generalized problem with some of the traceable components, so we can find all the printers potentially affected.
Assembly Guide
Probably the most important document in the whole process, the Assembly Guide provides step by step guide for the worker. This grants all the Sigmas are assembled equally, no matter if the worker is new or it’s been working with us since the very first day. In addition, it points not only the jigs or tools needed, but also the verifications to do during the assembly and some warnings.
As explained before, the Sigma is built in different stages, so the Assembly Guide is divided in several chapters that can be redistributed if needed, increasing the efficiency and flexibility of the assembly line.
Jigs and Fixtures
The BCN3D Sigma is a high-precision equipment, so it is mandatory to assemble it meticulously. On the other hand, assembly time is a key factor we intend to reduce steadily. Both factors force us to design several jigs and fixtures to make sure the axes are properly aligned and the time needed to built a Sigma can be reduced day after day.
Quality Protocol
Once the Sigma is assembled, it’s time to verify it works perfectly. Every single printer undergoes a thorough Quality Protocol that checks its finish as well as its mechanical and electronic systems. Finally, the Sigma prints some test parts during approximately 25h.